Sintering process of high purity boron carbide ceramics
Sintering of boron carbide ceramics
1. Pressureless sintering
Boron carbide is a compound with strong covalent bonds, and its covalent bond ratio is as high as 93.94%. Therefore, the sintering performance is very poor. The pressureless sintering temperature without any additives is about 2300℃. The mechanism is the volume diffusion when the temperature is close to its melting point. The most important prerequisite for the densification of pure boron carbide is to use ultra-fine powder with an average particle size of less than 3um and low oxygen content. The sintering temperature and the obtained density of boron carbide are respectively: 2240~2300℃, 78%~ 86% density; 2440℃, greater than 90% density; 2510℃, sintered with finer powder, 99% density. Sintering under normal pressure not more than 2300℃, the relative density of boron carbide is not more than 90%, and it is prone to abnormal crystal grain growth and crystal surface melting. Increasing the specific surface area of boron carbide powder and reducing the average particle size can significantly increase the sintered density. Studies have shown that increasing the specific surface area and purity of the raw material powder can significantly promote the sintering process, reduce the sintering temperature, and increase the quality and density of sintering. When the specific surface area is greater than 16㎡/g, the sintering temperature can be reduced by 180℃, the relative density of the sintered body can reach more than 98%, the bending strength can reach 456MPa, and the hardness HV is 2790. The performance of the product is close to the level of hot-pressed products. The pressureless sintered boron carbide ceramic material without additives is a process method suitable for mass production of parts with complex shapes. However, due to the strict requirements for powder and the need to use ultra-high temperature sintering, its process parameters are difficult in mass production. Control, the performance of the product is also extremely unstable.
2. Pressureless sintering with additives
Adopt methods to increase the density of point defects or dislocations, increase the area of grain boundaries and increase the activation of volume diffusion, and densification can be achieved at lower temperatures: (1) The mechanical alloying method of high-energy ball milling is used to increase the ratio Surface area; 2) Put trivalent ions, such as aluminum or boron, to replace carbon, resulting in electron loss and vacancies; 3) Introduce some sintering aids to remove oxides on the surface of boron carbide particles to increase surface energy, such as adding aluminum carbide, Silicon carbide, carbon, or related compounds can prevent excessive grain growth. Other additives that provide Al are Al2C3, Al4C3, AIF3, etc., and fluoride or carbon can also be used as deoxidizers. Additives such as CrB2, TiB2, W2B5 can produce a pinning effect, and can also prevent grain growth. Using C as a sintering additive can effectively promote the sintering of boron carbide ceramics, so that boron carbide ceramics can achieve a higher mass density at a lower sintering temperature. When the C mass fraction is about 3%, the relative density can reach the maximum, that is, the relative density is 92.7%, and the bending strength can reach 403MPa. The modulus of elasticity increases with the relative density. Fracture toughness is basically independent of relative density. Combined additives, including the addition of carbon and metal borides or carbides, can simultaneously deoxidize carbon and promote metal diffusion, as well as refining grains and enhancing the second phase. Pressureless sintering adds TiB2 with a volume fraction of 20% boron carbide, and uses C and Ni as sintering aids. When the temperature is raised to 1600°C, a 94% dense boron carbide product is obtained, and no chemical reaction occurs between the two phases. , Only the liquid phase infiltration of the sintering aid. The pyrolysis of phenolic resin into amorphous carbon and the in-situ pyrolysis of organic additives are current research hotspots. The advantage of this method is that it can improve the uniformity of carbon distribution and obtain ultra-fine average grain size.
3. Hot pressing, hot isostatic pressing (HIP) sintering
Hot pressing sintering is to pack the powder in the cavity of the mold, heat the powder to a sintering temperature or lower while pressing, and sinter it into a dense and uniform B4C product in a short time. Hot pressing sintering is enhanced sintering. Hot pressing causes particle rearrangement and plastic flow, strain-induced twinning, grain boundary slip, creep, and the combination of volume diffusion and recrystallization in the later stages of material migration. Hot-pressing sintering uses the effect of pressure and surface energy as the driving force for sintering, so hot-pressing can reduce the sintering temperature of ceramic sintering and increase the density of the sintered body. Its advantages are: good plasticity of the powder under high temperature conditions, low forming pressure, low deformation resistance, low sintering temperature, faster sintering speed, densification of refractory materials, fine grains, excellent microstructure, etc.; disadvantages: counter-pressure The material requirements of the mold are high, the process is complicated, the production scale is small, and the yield is low. Hot isostatic pressing (HIP) sintering is to use inert gas such as Ar as the medium to transfer pressure, and put the boron carbide powder compact or the powder packed in the sheath into a high-pressure container, so that the powder can withstand equal pressure and high temperature. Lower the sintering temperature, avoid the growth of grains, and obtain high-density boron carbide ceramic products. Compared with the hot pressing method, it can subject the material to isotropic pressure, so the microstructure of the ceramic is more uniform. The disadvantage is that the equipment cost is high and the size of the workpiece to be processed is limited.
4. Spark plasma sintering (SPS)
The spark plasma sintering method is a new rapid sintering process. It is to pass an instantaneous, intermittent, high-energy pulse current into a mold containing boron carbide powder, and plasma discharge can be generated between the powder particles to purify the powder. Activation, homogenization and other effects. Traditional hot press sintering is mainly caused by plastic deformation caused by pressure and Joule heat generated by electricity to promote the sintering of boron carbide. In addition to the above effects, the sintering process of spark plasma is used on the compacted particle sample. The DC pulse voltage generated by a special power supply is applied, and the instantaneous discharge plasma is effectively used to uniformly self-heat the inside of the sintered boron carbide and activate the particle surface, so it has high thermal efficiency and can be used in a relatively short time. Within time, the sintered boron carbide will be dense.
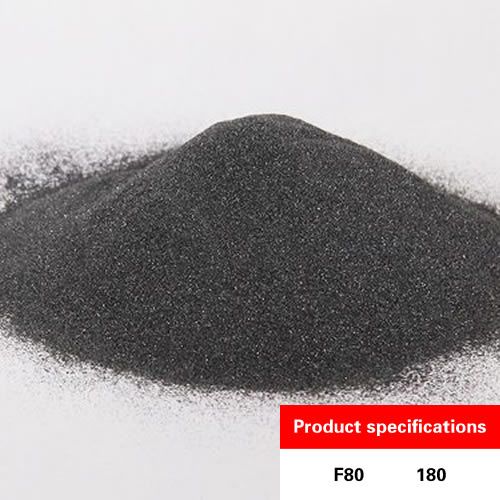
5. Liquid phase sintering
Sintering is the sintering of compacts or powders of two or more components in a liquid phase under the condition that the low melting component melts or forms a low melting eutectic. The liquid phase causes the material to migrate faster than the solid phase, and finally the liquid phase will fill all the pores in the sintered body, so a product with high density and good performance is obtained.
6. Toughening of boron carbide
The current research on boron carbide is mainly devoted to the toughening of boron carbide ceramics. The main toughening methods include: grain size refinement and toughening, transition metal boride particles second phase toughening, transition metal carbide particles toughening, Toughening of metals, toughening of carbon and carbides. The trend of toughening research is mainly in-situ autogenous toughening method and precursor pyrolysis method. In addition, there is also a pyrolytic nanoparticle toughening process represented by polycarbosilane, which forms a solid solution between large-diameter B4C and The formation of intragranular nanostructures accelerates the dissolution-deposition process during material sintering, promotes the densification of materials, and also improves the grain boundary structure of B4C ceramics, both in terms of uniformity and densification. Advantage. 3. Application of boron carbide ceramics. Boron carbide has a series of excellent properties: low density, high hardness, stable chemical properties, and boron carbide has a strong ability to absorb neutrons. Based on these excellent characteristics, boron carbide has It has been widely used in many fields.